Thermoplastic Elastomers (TPEs) are a class of polymers that, within their design limits, behave like thermoset rubber but that, above their melt or softening temperatures, are melt processable via thermoplastic processing methods and, unlike thermoset rubber, can be easily reprocessed and remolded. The ability to process these materials with thermoplastic methods allows for design and fabrication freedom that thermoset rubber does not offer.
All TPEs are composed of crystalline and amorphous domains. Some are blends or alloys of crystalline and amorphous polymers, some are block co-polymers comprised of blocks of crystalline and amorphous domains along the same polymer chain. It is the crystalline domains that act as the “heat-fugitive cross-links” that give TPEs their thermoplastic character and the amorphous domains that give them their elastomeric character. The crystalline domains are typically referred to as the “hard” phase and the amorphous domains as the “soft” phase. While both phases contribute to the overall physical and mechanical properties of a TPE, some key properties may be associated with one phase or the other thereby guiding the selection or design of a TPE compound.
“Hard Phase” — The plastic properties:
- Processing temperatures
- Continuous use temperature
- Tensile strength
- Tear strength
- Chemical and fluid resistance
- Adhesion to inks, adhesives, and over-molding substrates
“Soft Phase” — The elastomeric properties:
- Lower service temperature limits
- Hardness
- Flexibility
- Elongation
- Compression set and tensile set
Industry has typically rated the various TPE technologies on a cost vs. performance basis. This is a convenient way of classifying materials but it can be very misleading because performance should be defined by the requirements of the application, rather than a standard property set, and the performance — price curve will vary depending upon the performance criteria of interest. In our section Choosing the Correct TPE, we list some of the criteria that RTP Company uses to narrow down and select the best TPE for an application.
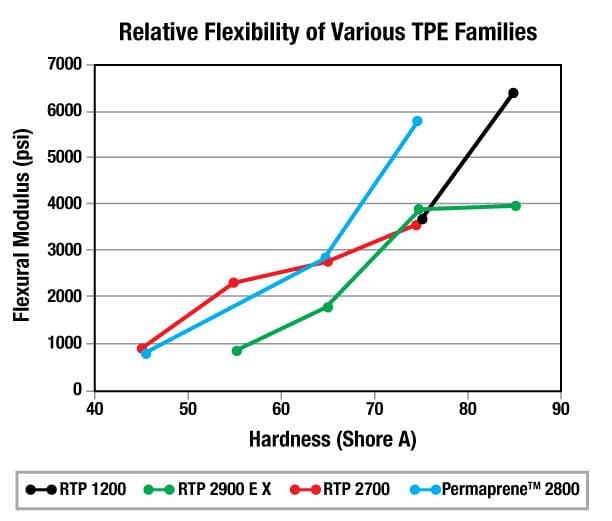