Our tribology experts provide Wear and Friction Resistant solutions for optimal performance of mating and moving parts. We have compiled extensive data on our large portfolio of materials designed to solve a number of wear- and friction-related issues so that your plastic applications operate smoothly and quietly!
We offer unbiased information to help you:
Determine the Right Wear Solution
Determine Additional Properties
We are singularly focused on finding the precise solution to fit the needs of your thermoplastic part or component. Our compounds are formulated to balance the correct base polymer selection with the appropriate Wear and Friction Resistant technology to meet your end-use requirements. In addition, structural reinforcement, static protection, flame retardance, and color properties can be combined into a single material! For more information, contact your local RTP Company representative.
Understanding Wear Principles
Successful Applications
- Bearings, slides, gears, and cams — Keep moving parts free of external grease and lubricants.
- Pump impellers — Save money and energy by using lightweight, injection molded thermoplastics rather than machined metal to significantly lower start-up torque.
- Gears — Improve resistance to repeated flexural bending, a primary cause of tooth failure.
- Bushings and rollers — Reduce noise in material handling systems and accommodate cleanroom or washdown environments.
- Sliding components — cover panels, doors, and latches on consumer electronics.
Does your application operate at high pressures and velocities (PVs)? And/or at high temperatures? Check out our Ultra Wear materials , which are engineered for these conditions!
For more information about specific Wear and Friction Resistant solutions, select from the list of common issues below:
With the release of EPA guidelines and state regulations regarding PFAS, one way to reach compliance is to utilize RTP Company’s environmentally conscious solutions: All Polymeric Wear Alloy (APWA) Compounds or Abrasion Resistant (ABR) Compounds. These materials offer exceptional wear and friction resistance without PTFE or PFOA additives.
Replace oils and grease applied in messy secondary operations with our internally lubricated plastics.
External lubricants such as silicone, PFPE oil, grease, or solid lubricants, can be replaced with one of these internally lubricated solutions:
- All-Polymeric Wear Additive (APWA)
- Perfluoropolyether oil (PFPE)
- Polytetrafluoroethylene (PTFE)
- Silicone (Si)
- Molybdenum disulfide (Moly)
- Graphite
Our internally lubricated compounds provide optimal performance of mating and moving parts, without the issues of external lubricants. Your local RTP Company representative can assist you in selecting the right internally lubricated compound for your application.
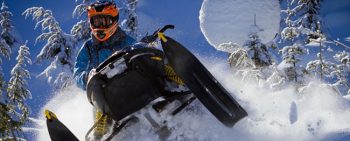
Many manufacturers turn to UHMWPE* to solve abrasion issues. However, this material is only available as stock shapes for machining of finished parts.
At RTP Company, we formulate Abrasion Resistant Compounds that minimize abrasion as well as UHMWPE can, but are designed specifically for injection molding, thereby opening up a whole new realm of design possibilities to solve abrasion issues!
*Ultra-High Molecular Weight Polyethylene
Learn more about the benefits of our Abrasion Resistant Compound Technology by downloading our Innovation Bulletin.
Reduce Stiction, or “stick-slip phenomenon” by selecting materials based on our Glide FactorSM data.
Stiction is the term used to describe a part that repeatedly slips and starts moving, then stops moving. High frequency stick-slip (stiction) often leads to audible squeaking.
With custom engineered compounds, stiction issues are “tunable” in controlled movement devices such as single-use injection devices, locks and latches, consumer packaging, and industrial doors and windows.
Learn more about plastic-onplastic friction applications for single-use medical devices by downloading our “Low Friction Plastic Technology for Single-Use Drug Delivery Devices” white paper.
Our Ultra Wear Compounds can help your application withstand high temperatures, pressure, velocity, chemicals, and demanding tolerances. These compounds are based on resins with inherent heat and chemical resistant properties, which are then formulated with additives and fillers to create compounds to solve multiple issues using one material.
Noises like BSR can be an unintended and undesired result of tightly clustered plastic components combined with movement and vibration.
Our engineers have developed a selection of Noise Reducing Compounds, specially formulated to optimize performance and minimize noise issues.
Scratching and marring on the surface of a plastic product can unintentionally damage its perceived high value. Scratch and mar can happen before or during shipping, or they can be caused by impact, rubbing, scraping, abrasion, or erosion of high contact parts.
Enhance product quality and increase end-use customer satisfaction with our Surface Protection (SPR) Compounds. These unique compounds provide:
- Improved scratch and mar resistance
- Improved surface feel
- Consistent slip
- Easy ejection during injection molding cycle
- Reduced surface roughness or die lines in extruded or blow molded surfaces
Learn more about the benefits of our Surface Protection Compound Technology by downloading our Innovation Bulletin.
Our wear- and friction-resistant compounds can incorporate internal lubricants to reduce wear and friction, thereby lengthening the service life of your applications and reducing processing costs.
To learn more, contact your local sales engineer!
Download a copy of our Wear Resistant brochure today!
Learn more about the benefits of Wear and Friction Resistant Compounds and the process of having a specialty compound formulated for your application’s requirements.