For more than 35 years, our engineers have been providing precise thermoplastic solutions for the automotive industry, ranging from high volume engineered materials to high tech specialty compounds. We support the industry’s commitment to sustainability by formulating thermoplastic compounds that make good sense for electric and autonomous vehicles, as well as their charging stations.
Because electric and autonomous vehicles have different requirements than internal combustion engine vehicles, the types of materials used can be very different than those that have been used historically… so we have a variety of options! Our materials are specially formulated to enhance and improve parts that are used in electric vehicles, autonomous vehicles, and charging stations, with benefits such as:
Strength
Performance
Lighter weight
Flame retardancy
Reduced VOCs
Better efficiency
Cost reduction
Applications
Click on any of the hot spots shown above to learn more about the technologies we offer for your applications. If you have any questions or would like additional information, please contact your local RTP Company representative or call us at (507) 454-6900.
RTP Company Technologies
Our Electromagnetic Interference (EMI) Shielding Compounds offer reliability and value in a wide range of applications where electromagnetic compatibility is required. Shielding provides protection for sensitive components from incoming EMI and/or prevents excessive emissions of EMI to other susceptible equipment.
Typically, EMI shielding compounds utilize stainless steel fiber or nickel-coated carbon fiber in a thermoplastic matrix to provide the necessary shielding. These compounds can also incorporate flame retardant additives, wear additives, reinforcements, and colorants in a single custom material solution to meet the requirements of your application.
Housings for radar boxes, GPS module enclosures, sensors, and cameras require EMI shielding to prevent signals from being mixed or interrupted. EMI Compounds can provide this protection and help to ensure the proper function of these sensitive components.
Description
Electrically conductive or EMI absorbing PP, PA, PBT,PC/ABS
Key Characteristics
Consistent EMI shielding effectiveness up to 90+ dB
Benefits
Integrated, molded-in shielding properties
Metal-to-plastic weight savings
Cost reduction
Typical Applications
Motors
Sensor and Camera housings
Control modules
Internal charging station parts requiring electrical current management
Property Comparison: EMI Shielding Compounds Shielding Effectiveness (SE) @ 2mm Thickness
* EMI Test Method: ASTM D4935
Technology A* | Technology B* |
---|---|
High SE | High SE |
Ductile | High Modulus |
Unreinforced | Fiber Reinforced |
Technology C* | Technology D* |
---|---|
Moderate SE | Moderate SE |
Ductile | High Modulus |
Unreinforced | Fiber Reinforced |
Technologies A-D are available in a wide variety of base polymers, such as PP, PBT, PA66, PC, ABS, and more.
Although flammability is not often a concern with conventional gas powered vehicles, electrical and autonomous vehicles do require a fresh approach to passenger safety. Most thermoplastics utilized in the automotive industry today are inherently flammable, and therefore require an additive package to meet industry flame standards such as UL94 V-0; in addition, they must function well in the end application.
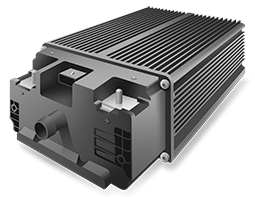
Batteries and their components benefit from Flame Retardant Compounds to help meet safety regulations and improve passenger safety.
Description
PP, PA, PBT
Key Characteristics
HB, V1, V2, V0, 5VB, and 5VA
Benefits
Risk mitigation
Colorable (safety orange, for example)
Typical Applications
LI Ion batteries
High voltage connectors
Parts with rating requirements
Battery Components: Housings, Frames, Plates, Trays
Formula | Description | UL 94 Flammability | Tensile Strength (MPa) | Flexural Modulus (GPa) | Charpy Notched Impact (kJ/m2) | HDT @ 1.82 MPa (°C) | Density | Filler Content |
---|---|---|---|---|---|---|---|---|
RTP 199 X 135008 A | PP – Glass Fiber – FR | V-0/5VA | 80 | 7.2 | 8.2 | 145 | 1.50 | 30 |
RTP 199 X 151875 A | PP – Unfilled – FR | V-0 | 25 | 1.1 | 5.8 | 52 | 1.00 | N/A |
RTP 199 X 156119 B | PP – Mineral – FR | V-0/5VA | 27 | 2.9 | 3 | 70 | 1.35 | 20 |
RTP 199 X 163680 | Glass Fiber Reinforced FR V-0 PP | V-0 @ 1.5mm | 60 | 6.5 | 10.0 | 135 | 1.32 | 30% GF |
RTP 299 X 164401 A | Glass Fiber Reinforced FR V-0 Nylon 6,6 | V-0 @ 0.8mm | 135 | 8.8 | 7.0 | 240 | 1.37 | 25% GF |
RTP 299 A X 163684 | Glass Fiber Reinforced FR V-0 Nylon 6 | V-0 @ 0.8mm | 130 | 10.0 | 10.0 | 216 | 1.44 | 30% GF |
RTP 299 K X 138337 C | PARA – Glass Fiber – FR | V-0/5VA | 193 | 15.9 | 11.5 | 210 | 1.57 | 40 |
RTP 299 K X 138337 E | Glass Fiber Reinforced FR V-0 PARA | V-0 @ 0.5mm | 214 | 20.7 | 20.0 | 210 | 1.69 | 50% GF |
RTP 399 X 143586 | PC – Transparent – Unfilled – FR | V-0/5VA | 69 | 2.7 | 12.2 | 125 | 1.24 | N/A |
RTP 2099 X 150722 A | PA Alloy – Glass Fiber – FR | V-0/5VA | 131 | 9.3 | 17 | 188 | 1.56 | 30 |
RTP 4099 X 163681 | Glass Fiber Reinforced FR V-0 PPA | V-0 @ 0.8mm | 160 | 11.0 | 7.0 | 280 | 1.45 | 30% GF |
Electrical Components: High Voltage Connectors, Terminal Covers, Telecommunication Housings
Formula | Description | UL 94 Flammability | Tensile Strength (MPa) | Flexural Modulus (GPa) | Charpy Notched Impact (kJ/m2) | HDT @ 1.82 MPa (°C) | Density | Filler Content |
---|---|---|---|---|---|---|---|---|
RTP 199 X 134952 B | PP – Mineral Filled – FR | V-0/5VA | 22 | 2.2 | 4.5 | 70 | 1.31 | 15 |
RTP 199 X 137777 D | PP – Unfilled – FR | V-0 | 31 | 1.4 | 2.3 | 55 | 1.02 | N/A |
RTP 1099 X 149490 | PBT – Glass Fiber – FR – Low Warp | V-0/5VA | 134 | 9.5 | 8.8 | 204 | 1.63 | 30 |
RTP 1099 X 156121 A | PBT – Glass Fiber – FR | V-0/5VA | 136 | 9.7 | 8 | 210 | 1.63 | 30 |
Outdoor Components: Connectors, In Cable Circuit Breakers/Control Boxes, Charging Station Housings
Formula | Description | UL 94 Flammability | Tensile Strength (MPa) | Flexural Modulus (GPa) | Charpy Notched Impact (kJ/m2) | HDT @ 1.82 MPa (°C) | Density | Filler Content |
---|---|---|---|---|---|---|---|---|
RTP 199 X 138253 A | PP- Unfilled UV – FR | V-0 | 24 | 1.2 | 47 | 52 | 1.04 | N/A |
RTP 2099 X 143976 D | PC/PBT – Unfilled – UV – FR | V-0/5VA | 48 | 2.1 | 48 | 88 | 1.29 | N/A |
Underhood Components: Engine Covers, Electrical Components
Formula | Description | UL 94 Flammability | Tensile Strength (MPa) | Flexural Modulus (GPa) | Charpy Notched Impact (kJ/m2) | HDT @ 1.82 MPa (°C) | Density | Filler Content |
---|---|---|---|---|---|---|---|---|
RTP 299 X 150941 A | PA 66 – Glass Fiber – FR | V-0 | 125 | 7.0 | 6.5 | 235 | 1.56 | 15 |
RTP 299 X 156120 A | PA 66 – Glass Fiber – FR | V-0 | 150 | 9.5 | 6.2 | 245 | 1.65 | 25 |
RTP 299 A X 157486 A | PA 6 – Glass Fiber – FR | V-0 | 125 | 7.0 | 15 | 200 | 1.54 | 15 |
Our Structural Compounds provide solutions in applications requiring excellent mechanical and/or thermal performance.
Short Glass Fiber (SGF) Compounds – chopped glass fiber provides strength and stiffness to our SGF compounds, which provide good, general purpose reinforcement.
Very Long Fiber (VLF) Compounds – in addition to the improvement in strength and stiffness versus SGF Compounds, VLF Compounds provide improved impact strength and are commonly used for metal replacement.
Carbon Fiber (CF) Compounds – our CF Compounds provide tremendous stiffness without adding significant weight to a vehicle. These high end materials, which are commonly used in aerospace, are finding broader use for lightweighting in electric and autonomous vehicles.
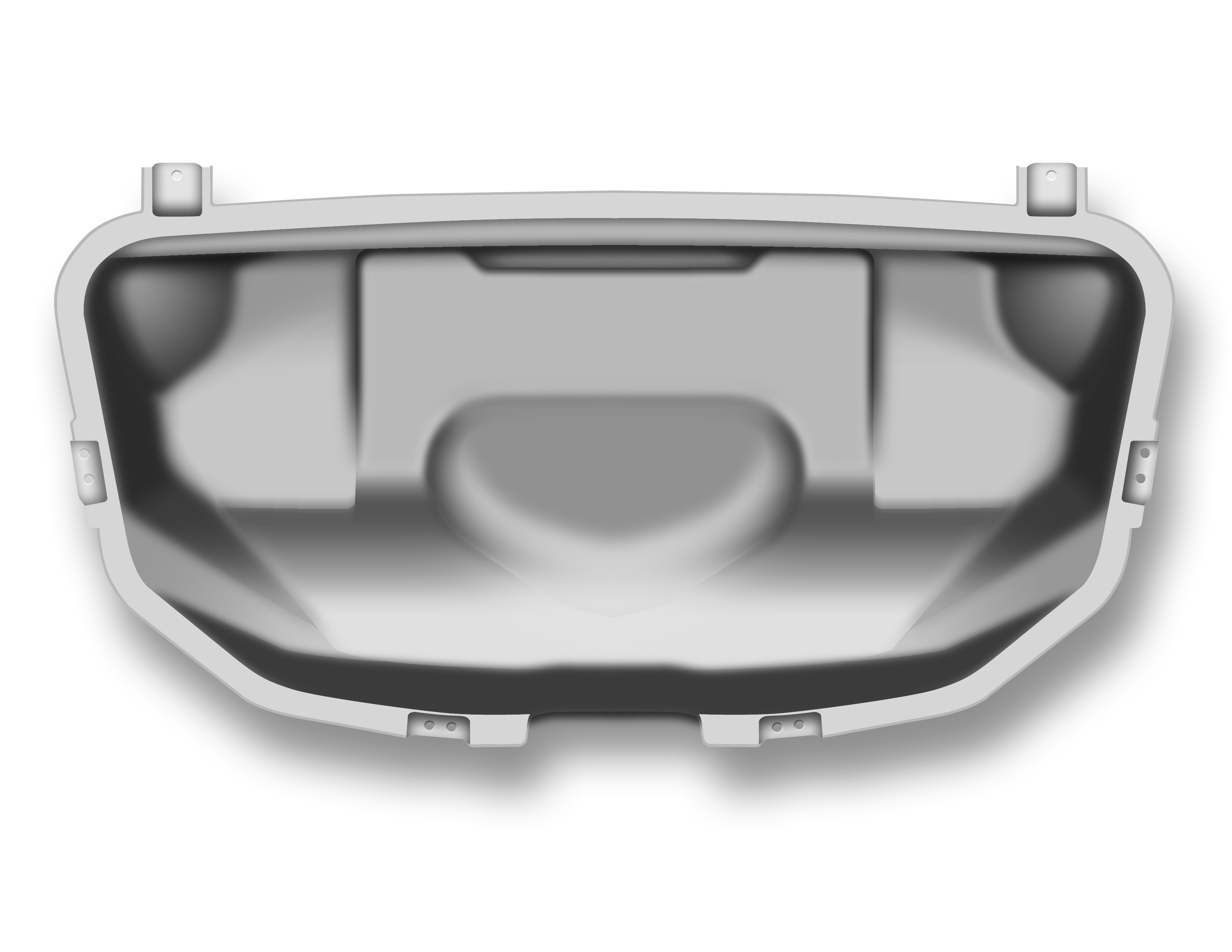
The “frunk”, or storage space under the front hood of an electric or autonomous vehicle, can be made from VLF Compounds for excellent durability and impact.
Description
Long Glass/Short Glass Fiber PP, PA, PBT; Carbon Fiber (CF) Compounds; ASA Alloys
Key Characteristics
Provide outstanding impact resistance, creep resistance, and aesthetic value
Benefits
Dimensional stability
Durability
Excellent for metal replacement
Reduce part weight
Colorable
Typical Applications
Battery plates
LI Ion battery housing cover
Frunk
Camera brackets/Sensor housings
Instrument panels
Interior trim
Outdoor housings and base units for charging stations
RTP Company Material Options | |||||||
---|---|---|---|---|---|---|---|
RTP 299 A X 143325 A | RTP 299 A X 149343 A | RTP 199 X 154150 B | RTP 199 X 70815 |
RTP 199 X 70836 A | |||
Property | Method | Unit | PA6 30% SGF | PA6 30% SGF Low Density | PP 20% CF | PP 30% VLF | PP 40% VLF |
Density | ISO 1183 | g/cm3 | 1.35 | 1.22 | 1.00 | 1.13 | 1.20 |
Tensile Strength | ISO 527 | MPa | 180 (113) | 167 (115) | 105 | 110 | 130 |
Flexural Modulus | ISO 178 | MPa | 9500 | — | 9233 | 6500 | 8500 |
Charpy Impact, Notched | ISO 179/1eA | kJ/m2 | 13 (15) | 10 (12) | 4.0 | 21 | 25 |
*All values Dry As Molded except those in parentheses, conditioned 23 °C, 50% RH to equilibrium.
For applications that require aesthetics, UV protection, and weatherability, we formulate ASA Alloys that provide high gloss, colorability, and UV performance. In addition, these alloys provide higher chemical resistance and thermal stability versus standard ABS, making them an excellent choice for thermoplastic housings on charging stations.
UV Resististance
Property | ABS | PC/ABS | PP | PA | ASA |
---|---|---|---|---|---|
UV Resistance | POOR | POOR | BETTER | BETTER | BEST |
Our high temperature compounds are formulated to withstand high heat environments, making them an excellent choice for electric motors, battery systems, and mating connectors. Made from resins that inherently offer better mechanical performance and both wear and chemical resistance, we can also tailor these products to meet specific application requirements. By selecting from a broad range of polymer and additive combinations, we can provide the precise color, mechanical function, wear resistance, dimensional stability, conductivity, and regulatory requirements of your application in a single, cost optimized solution.
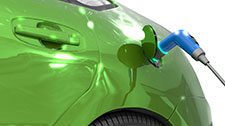
High Temperature Mineral Filled Compounds provide improvements in dimensional stability and stiffness in high temperature environments over unmodified resin.
Description
PSUL, PES, PPSU, PEI, PEEK, PPA, PPS, TPI, HTN
Key Characteristics
Withstand high heat environments and higher continuous use temperatures
Benefits
Consolidate parts
Reduce part weight
Inherent wear and chemical resistance
Provide design freedom
Typical Applications
Motors
Battery systems
Mating connectors
Color can be used in many ways, including to draw attention, communicate instructions, enhance safety features, build brand awareness, create special effects, and more. Choose from our standard color palette or request a custom color match! Our color compounds are available in Precolor, Masterbatch, or Cube Blend, and can be enhanced with functional additives such as UV protection packages to prevent fade and deterioration for applications such as exterior housings or charging stations.
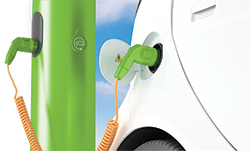
Our Color Engineering Team uses high end spectrophotometers and their extensive knowledge to ensure your thermoplastic custom color is precise and can withstand harsh outdoor elements.
Description
Precolor, Masterbatch, Cube Blend
Key Characteristics
100% color matched UV stable
Benefits
Harmony with interior trim color
Special effects like metallics
Typical Applications
Interior hard trim
UV protected color for charging stations
From off-the-shelf resins to complex custom compounds, our TPEs provide unique benefits for electric and autonomous vehicles, including improved ergonomics, noise reduction, and superior sealing ability. Available in durometers ranging from 10 shore A to 65 shore D, they are commonly used in automotive parts such as seals, gaskets, air deflectors, handles, and grips. Our Nylabond™ and Polabond® materials are bondable to various substrates including Nylon, ABS, PC, PC/ABS and other engineering resins, while our high temperature TPV technology bonds well to nylon substrates for applications used in extreme environments.
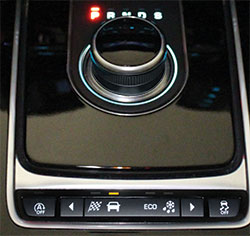
Our NylabondTM nylon bondable TPVs can be overmolded to a rigid substrate to improve part integrity, eliminate the need for adhesives, and enhance grip performance for parts like gear knobs.
Description
Nylabond™ Nylon Bondable TPV
Key Characteristics
55A to 85A Durometer
Benefits
Sealing
Ergonomics
Flexibility
Typical Applications
Seals
Air deflector
Miscellaneous
Our Wear and Friction Resistant compounds solve a number of issues, including noise, abrasion, friction, and scratching/marring. Noise is particularly important in the case of electric and autonomous vehicles, since the expectation is a quiet cabin. Molded parts made from our wear and friction resistant compounds can be internally lubricated and provide noise reduction between mated or sliding parts. In addition, they provide protection from scratching and marring of surfaces, as well as excellent oxidation and corrosion resistance for handles, latches, gears, bushings, and more.
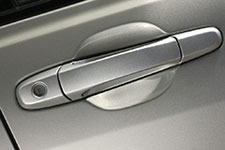
Our wear and friction resistant compounds can reduce noise, provide scratch protection, and extend the service life of parts like vehicle door handles.
Description
Internally lubricated compounds; PTFE, Graphite, Moly, Silicone
Key Characteristics
Reduce wear and friction
Benefits
Eliminate grease and squeaks
Extend product life
Typical Applications
Latches
Gears and bushings
Seals and gaskets
Several divisions of RTP Company provide special materials designed with the automotive market in mind. For example, we can provide reclaimed fiber materials, ideal for cargo/frunk liners and mats, or diffused lighting compounds for dashboard controls.
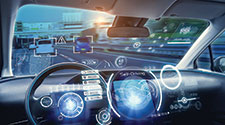
Only RTP Company offers the widest selection of material solutions for every aspect of electric and autonomous vehicles!
Description
Sheet, film, and fiber materials
Key Characteristics
Varies by material
Benefits
One source for a wide range of EV materials
Typical Applications
Trunk lining
Floor mats
Lighted control panels